How New Machinery Can Improve Your Business?
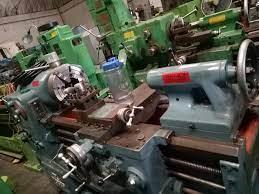
The new machinery on the market will come with the latest technology. This can help employees work smarter and faster, which can increase productivity throughout your entire company.
New equipment also typically comes with warranties and vendor support to help avoid downtime. These services may not be offered for used machines, which can save you a significant amount of money on a new piece of equipment.
Reliability
Reliability refers to how well a New machinery or piece of equipment performs over time. This includes its performance against the aforementioned environmental factors, as well as the ability to overcome failures and disruptions.
Reducing the frequency of unscheduled downtime results in less production waste, fewer defective products, and more consistent delivery dates. It also reduces the amount of money a company spends on maintenance, repairs, and replacement parts. Achieving world-class reliability requires that senior management set realistic goals and communicate them throughout the facility. This will involve all departments, from engineering and design to procurement and operations. Each department will play its own role in keeping production running smoothly, but they all can help by making reliability a priority. This can be done by establishing a budget for equipment maintenance, setting up a preventive maintenance schedule, and implementing best practices. All of these things will increase the overall reliability of equipment. However, the most effective way to improve equipment reliability is by reducing external factors that cause failures and creating redundancies.
Technology
Machines that collect and analyze data help companies reduce costs by identifying maintenance issues before they occur. Unplanned downtimes cost businesses billions each year, but predictive maintenance technology can lower those numbers dramatically by preventing breakdowns and increasing equipment uptime.
New equipment is often designed with specific jobsites and operator needs in mind, including features that boost productivity and safety. For example, earthmoving equipment manufacturers have introduced one-of-a-kind options like all-around cameras and grade control systems for excavators and transparent buckets and onboard weighing technologies for wheel loaders. Whether it’s improving quality or cutting costs, rapid technology developments significantly affect the manufacturing industry. However, these upgrades don’t come cheap. Purchasing used machinery can save you tens of thousands and still provide the same tax benefits, financing opportunities and warranties as a brand-new piece of equipment. The money saved can be redirected towards specialized tooling, raw materials or additional shop staff.
Maintenance
While buying new machinery requires a substantial investment, it will save you money in the long run. This is because new equipment will require fewer repairs initially than older machinery. In addition, it is a more efficient use of resources and can reduce operational downtime. Individuals with expectations to know about circuit breakers for sale and other details can feel free to visit here.
Maintenance techniques are crucial to a manufacturing firm’s profitability and productivity. However, there is little literature and data on the costs and losses associated with different machine maintenance methodologies. The best way to prevent unplanned machine downtime is to implement a maintenance plan. A good maintenance plan will include both proactive and reactive maintenance strategies. Proactive maintenance involves following the manufacturer’s recommendations and recording all maintenance activities. This will help to ensure that all equipment is serviced regularly and avoids unplanned downtime. In contrast, reactive maintenance waits until a machine breaks down before making repairs. This type of maintenance can be expensive and cause delays in production.
- Art
- Causes
- Crafts
- Dance
- Drinks
- Film
- Fitness
- Food
- Juegos
- Gardening
- Health
- Home
- Literature
- Music
- Networking
- Other
- Party
- Religion
- Shopping
- Sports
- Theater
- Wellness