Precision Engineering for Uninterrupted Power Supply
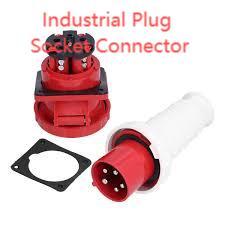
Effective production workflows depend on a Industrial Plug Socket Connector integrated seamlessly into power distribution networks to handle high currents and maintain robust electrical connections.
Tailoring Connectors to Load Profiles
Every machine in a facility exhibits unique power demands, from steady-state currents to brief inrush peaks when motors start. Engineers must calculate both continuous and peak current values to choose connectors rated appropriately. Undersized components can overheat, causing insulation breakdown or contact failure, while oversized connectors add unnecessary bulk and cost. By matching connector specifications—such as amperage rating, voltage class, and phase configuration—to actual load profiles, plants optimize energy efficiency and reduce lifecycle expenses associated with premature replacements.
Material Durability and Protective Coatings
Industrial environments expose equipment to dust, moisture, oils, and temperature extremes. Connector housings fashioned from glass-reinforced nylon or marine-grade stainless steel resist mechanical shock and chemical corrosion. Internally, contacts coated with silver or nickel layers ensure consistent conductivity and prevent oxidation. Some manufacturers apply specialized sealants or hydrophobic coatings to further guard against ingress and chemical attack. Choosing materials and coatings based on site-specific hazards—such as salt spray or caustic cleaners—extends service intervals and minimizes unplanned downtime.
Mennekes Solutions for Simplified Maintenance
Major brands like Mennekes offer modular connector systems that expedite inspection and replacement. Their components often feature color-coded phases, captive O-rings, and tool-free locking mechanisms that reduce installation errors and speed up routine checks. Visual engagement indicators confirm secure mating, while hinged covers seal unused receptacles against contaminants. Mennekes also provides software tools for asset tracking, allowing maintenance teams to log usage cycles and predict end-of-life for each unit, facilitating just-in-time procurement and preventing shortages.
Installation Guidelines and Safety Procedures
Proper installation underpins connector reliability and operator safety. Mount receptacles on smooth, vibration-damped surfaces and apply recommended torque settings to coupling rings to prevent loosening. Use strain-relief clamps to avoid cable fatigue at the termination point. Always de-energize circuits before mating or unmating connectors, and follow lockout-tagout protocols. Periodically inspect gaskets and contact faces for wear, cleaning with approved solvents and applying dielectric grease sparingly when specified. These practices preserve contact integrity and reduce arc-flash hazards.
Future Trends in Connectivity Innovation
As factories adopt Industry 4.0 principles, connectors evolve to include embedded sensors that monitor temperature, voltage drop, and mating force in real time. Data streams integrate with SCADA and predictive-maintenance platforms, alerting teams to anomalies before failures occur. Plug-and-play designs with hot-swap capabilities support rapid line reconfiguration, enabling manufacturers to switch between product runs with minimal delay. Embracing these smart connectivity solutions ensures that power distribution infrastructure remains agile, efficient, and aligned with digital transformation goals.
For detailed specifications and ordering information, visit www.nante.com.